အောက်ပါတို့သည် SMT (surface mount technology) မှ DIP (dual in-line package), AI detection နှင့် ASSY (assembly) အထိ ပြီးပြည့်စုံသော ထုတ်လုပ်မှုလုပ်ငန်းစဉ်တစ်ခုဖြစ်ပြီး လုပ်ငန်းစဉ်တစ်လျှောက်လုံး နည်းပညာဆိုင်ရာဝန်ထမ်းများမှ လမ်းညွှန်မှုပေးပါသည်။ ဤလုပ်ငန်းစဉ်သည် အရည်အသွေးမြင့်မားပြီး ထိရောက်သောထုတ်လုပ်မှုကိုသေချာစေရန် အီလက်ထရွန်းနစ်ကုန်ထုတ်မှုတွင် အဓိကချိတ်ဆက်မှုများကို အကျုံးဝင်သည်။
SMT → DIP → AI စစ်ဆေးခြင်း → ASSY မှ ကုန်ထုတ်လုပ်မှုလုပ်ငန်းစဉ်ကို အပြီးသတ်ပါ။
1. SMT (မျက်နှာပြင်တပ်ဆင်နည်းပညာ)
SMT သည် PCB တွင် surface mount components (SMD) ကို တပ်ဆင်ရန်အတွက် အဓိကအားဖြင့် အီလက်ထရွန်းနစ်ထုတ်လုပ်မှု၏ အဓိကလုပ်ငန်းစဉ်ဖြစ်သည်။
(၁) Solder paste ပုံနှိပ်ခြင်း။
စက်ပစ္စည်း- ဂဟေဆော်သည့် ပရင်တာ။
အဆင့်များ-
ပရင်တာခုံပေါ်ရှိ PCB ကိုပြင်ပါ။
သံမဏိကွက်မှတဆင့် PCB ၏ pads များပေါ်တွင်ဂဟေကပ်ထားသောကပ်ခြင်းကိုတိကျစွာပုံနှိပ်ပါ။
အော့ဖ်ဆက်၊ ပျောက်ဆုံးနေသော ပုံနှိပ်ခြင်း သို့မဟုတ် ထပ်နှိပ်ခြင်း မရှိကြောင်း သေချာစေရန် ဂဟေငါးပိပုံနှိပ်ခြင်း၏ အရည်အသွေးကို စစ်ဆေးပါ။
အဓိကအချက်များ-
ဂဟေငါးပိ၏ viscosity နှင့် thickness သည် လိုအပ်ချက်များနှင့် ကိုက်ညီရမည်။
စတီးကွက်များကို ပိတ်ဆို့ခြင်းမဖြစ်စေရန် ပုံမှန်သန့်ရှင်းရေးပြုလုပ်ရန် လိုအပ်ပါသည်။
(၂) အစိတ်အပိုင်းနေရာချထားခြင်း။
စက်ပစ္စည်း- စက်ကို ရွေးပြီး နေရာချပါ။
အဆင့်များ-
SMD စက်၏ feeder ထဲသို့ SMD အစိတ်အပိုင်းများကို ထည့်ပါ။
SMD စက်သည် နော်ဇယ်မှတဆင့် အစိတ်အပိုင်းများကို ကောက်ယူပြီး ပရိုဂရမ်အရ PCB ၏ သတ်မှတ်ထားသော အနေအထားတွင် တိကျစွာ နေရာချပေးသည်။
အော့ဖ်ဆက်မှု၊ မှားယွင်းသော အစိတ်အပိုင်းများ သို့မဟုတ် ပျောက်ဆုံးနေသော အစိတ်အပိုင်းများ မရှိကြောင်း သေချာစေရန် နေရာချထားမှု တိကျမှုကို စစ်ဆေးပါ။
အဓိကအချက်များ-
အစိတ်အပိုင်းများ၏ polarity နှင့် direction မှန်ကန်ရပါမည်။
အစိတ်အပိုင်းများပျက်စီးမှုမဖြစ်စေရန် SMD စက်၏ နော်ဇယ်အား ပုံမှန်ထိန်းသိမ်းထားရန် လိုအပ်သည်။
(၃) Reflow ဂဟေ
စက်ပစ္စည်း- ဂဟေမီးဖိုသို့ ပြန်ထွက်ခြင်း။
အဆင့်များ-
တပ်ဆင်ထားသော PCB ကို reflow ဂဟေမီးဖိုထဲသို့ ပို့ပါ။
ကြိုတင်အပူပေးခြင်း၊ အဆက်မပြတ် အပူချိန်၊ ပြန်ထွက်ခြင်းနှင့် အအေးပေးခြင်း အဆင့်လေးဆင့်ပြီးနောက်၊ ဂဟေငါးပိသည် အရည်ပျော်သွားပြီး ယုံကြည်စိတ်ချရသော ဂဟေအဆစ်တစ်ခုကို ဖွဲ့စည်းလိုက်သည်။
အအေးမိဂဟေအဆစ်များ၊ တံတားများ သို့မဟုတ် သင်္ချိုင်းကျောက်များကဲ့သို့ ချို့ယွင်းချက်မရှိစေရန် ဂဟေအရည်အသွေးကို စစ်ဆေးပါ။
အဓိကအချက်များ-
reflow ဂဟေ၏အပူချိန်မျဉ်းကွေးသည် ဂဟေငါးပိ၏ဝိသေသလက္ခဏာများနှင့် အစိတ်အပိုင်းများအလိုက် အကောင်းဆုံးဖြစ်အောင်ပြုလုပ်ရန် လိုအပ်သည်။
တည်ငြိမ်သော ဂဟေအရည်အသွေးသေချာစေရန် မီးဖိုအပူချိန်ကို ပုံမှန်ချိန်ညှိပါ။
(၄) AOI စစ်ဆေးခြင်း (အလိုအလျောက်အလင်းစစ်ဆေးခြင်း)၊
စက်ပစ္စည်း- အလိုအလျောက် အလင်းစစ်ဆေးရေးကိရိယာ (AOI)။
အဆင့်များ-
ဂဟေအဆစ်များ၏ အရည်အသွေးနှင့် အစိတ်အပိုင်းတပ်ဆင်ခြင်း တိကျမှုကို သိရှိရန် ဂဟေဆက်ထားသော PCB ကို Optically စကန်ဖတ်ပါ။
ပြုပြင်ပြောင်းလဲမှုအတွက် ယခင်လုပ်ငန်းစဉ်တွင် ချို့ယွင်းချက်များနှင့် အကြံပြုချက်များကို မှတ်တမ်းတင်ပြီး ခွဲခြမ်းစိတ်ဖြာပါ။
အဓိကအချက်များ-
PCB ဒီဇိုင်းအရ AOI ပရိုဂရမ်ကို အကောင်းဆုံးဖြစ်အောင် ပြုလုပ်ရန် လိုအပ်သည်။
ထောက်လှမ်းမှု တိကျသေချာစေရန် စက်ပစ္စည်းကို ပုံမှန်ချိန်ညှိပါ။
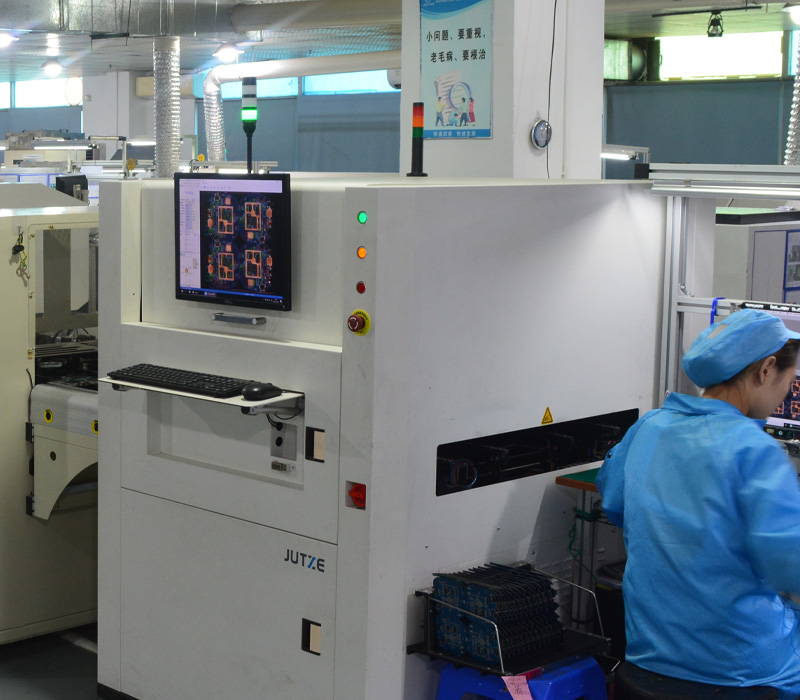
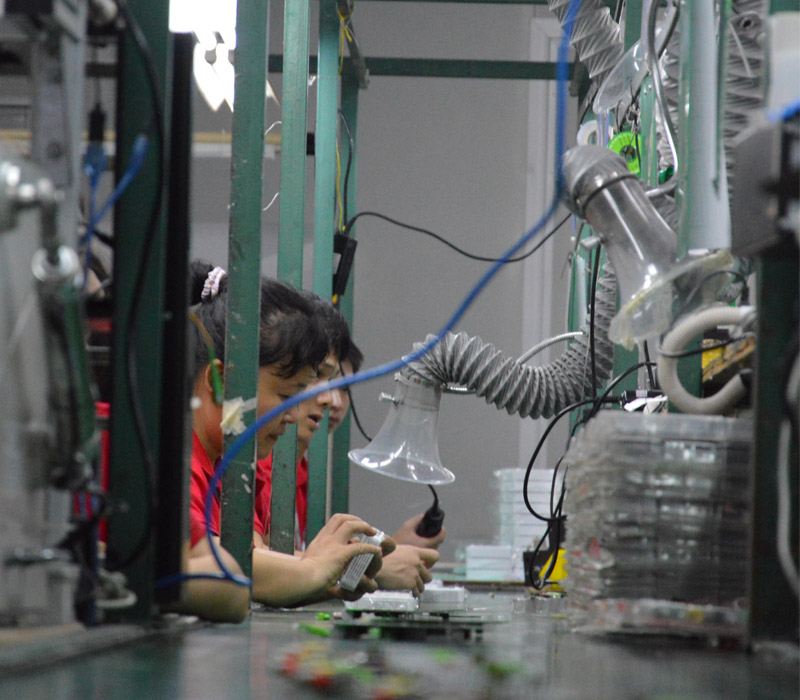
2. DIP (မျဉ်းနှစ်ကြောင်းအထုပ်) လုပ်ငန်းစဉ်
DIP လုပ်ငန်းစဉ်ကို အပေါက်မှတဆင့် အစိတ်အပိုင်းများ (THT) တပ်ဆင်ရန် အဓိကအသုံးပြုပြီး SMT လုပ်ငန်းစဉ်နှင့် ပေါင်းစပ်အသုံးပြုသည်။
(၁) ထည့်သွင်းခြင်း။
ပစ္စည်း- လက်စွဲ သို့မဟုတ် အလိုအလျောက် ထည့်သွင်းစက်။
အဆင့်များ-
အပေါက်ဖောက်ထားသော အစိတ်အပိုင်းကို PCB ၏ သတ်မှတ်ထားသော အနေအထားတွင် ထည့်သွင်းပါ။
အစိတ်အပိုင်းထည့်သွင်းခြင်း၏ တိကျမှုနှင့် တည်ငြိမ်မှုကို စစ်ဆေးပါ။
အဓိကအချက်များ-
အစိတ်အပိုင်း၏ pins များကို သင့်လျော်သော အရှည်အတိုင်း ဖြတ်တောက်ရန် လိုအပ်သည်။
အစိတ်အပိုင်း polarity မှန်ကန်ကြောင်း သေချာပါစေ။
(၂) လှိုင်းဂဟေ
စက်ပစ္စည်း- လှိုင်းဂဟေမီးဖို။
အဆင့်များ-
ပလပ်အင် PCB ကို လှိုင်းဂဟေမီးဖိုထဲသို့ ထည့်ပါ။
လှိုင်းဂဟေဖြင့် PCB အကွက်များသို့ အစိတ်အပိုင်းတံများကို ဂဟေဆက်ပါ။
အအေးမိဂဟေအဆစ်များ၊ ပေါင်းကူးခြင်း သို့မဟုတ် ဂဟေအဆစ်များ ယိုစိမ့်ခြင်း မရှိစေရန် ဂဟေအရည်အသွေးကို စစ်ဆေးပါ။
အဓိကအချက်များ-
PCB နှင့် အစိတ်အပိုင်းများ ၏ ဝိသေသလက္ခဏာများ အရ လှိုင်းဂဟေ၏ အပူချိန်နှင့် အမြန်နှုန်းကို ပိုမိုကောင်းမွန်အောင် ပြုလုပ်ရန် လိုအပ်ပါသည်။
ဂဟေအရည်အသွေးမထိခိုက်စေရန် ဂဟေရေချိုးခန်းကို ပုံမှန်သန့်ရှင်းရေးလုပ်ပါ။
(၃) Manual ဂဟေ
ချို့ယွင်းချက်များကို ပြုပြင်ရန်အတွက် လှိုင်းဂဟေပြီးနောက် PCB ကို ကိုယ်တိုင်ပြုပြင်ပါ။
စက်သုံးဂဟေအတွက် ဂဟေသံ သို့မဟုတ် လေပူသေနတ်ကို အသုံးပြုပါ။
3. AI ထောက်လှမ်းခြင်း (ဉာဏ်ရည်တု ထောက်လှမ်းခြင်း)
အရည်အသွေး ထောက်လှမ်းခြင်း၏ ထိရောက်မှုနှင့် တိကျမှုကို မြှင့်တင်ရန် AI ထောက်လှမ်းမှုကို အသုံးပြုသည်။
(၁) AI အမြင်အာရုံထောက်လှမ်းခြင်း။
ပစ္စည်း- AI အမြင်အာရုံခံစနစ်။
အဆင့်များ-
PCB ၏ High-definition ပုံများကို ရိုက်ကူးပါ။
ဂဟေချို့ယွင်းချက်များ၊ အစိတ်အပိုင်းကို နှိမ်နှင်းခြင်းနှင့် အခြားပြဿနာများကို ခွဲခြားသတ်မှတ်ရန် AI အယ်လဂိုရီသမ်များမှတစ်ဆင့် ပုံကို ပိုင်းခြားစိတ်ဖြာပါ။
စမ်းသပ်မှုအစီရင်ခံစာကို ဖန်တီးပြီး ထုတ်လုပ်မှုလုပ်ငန်းစဉ်သို့ ပြန်လည်ပေးပို့ပါ။
အဓိကအချက်များ-
AI မော်ဒယ်သည် အမှန်တကယ် ထုတ်လုပ်မှုဒေတာအပေါ် အခြေခံ၍ လေ့ကျင့်ပြီး ပိုမိုကောင်းမွန်အောင် ပြုလုပ်ရန် လိုအပ်ပါသည်။
ထောက်လှမ်းမှု တိကျမှုကို မြှင့်တင်ရန် AI algorithm ကို ပုံမှန် အပ်ဒိတ်လုပ်ပါ။
(၂) လုပ်ငန်းခွင်စမ်းသပ်ခြင်း။
စက်ပစ္စည်း- အလိုအလျောက် စမ်းသပ်ကိရိယာ (ATE)။
အဆင့်များ-
ပုံမှန်လုပ်ဆောင်ချက်များကိုသေချာစေရန် PCB တွင် လျှပ်စစ်စွမ်းဆောင်မှုစစ်ဆေးမှုများ ပြုလုပ်ပါ။
စမ်းသပ်မှုရလဒ်များကို မှတ်တမ်းတင်ပြီး ချွတ်ယွင်းနေသော ထုတ်ကုန်များ၏ အကြောင်းရင်းများကို ခွဲခြမ်းစိတ်ဖြာပါ။
အဓိကအချက်များ-
စမ်းသပ်မှုလုပ်ငန်းစဉ်သည် ထုတ်ကုန်လက္ခဏာများနှင့်အညီ ဒီဇိုင်းရေးဆွဲရန်လိုအပ်သည်။
စမ်းသပ်မှု တိကျသေချာစေရန် စမ်းသပ်ကိရိယာကို ပုံမှန် ချိန်ညှိပါ။
4. ASSY လုပ်ငန်းစဉ်
ASSY သည် PCB နှင့် အခြားအစိတ်အပိုင်းများကို ပြီးပြည့်စုံသော ထုတ်ကုန်တစ်ခုအဖြစ် စုစည်းခြင်းလုပ်ငန်းစဉ်ဖြစ်သည်။
(၁) စက်တပ်ဆင်မှု
အဆင့်များ-
PCB ကို အိမ်ရာ သို့မဟုတ် ကွင်းထဲသို့ ထည့်သွင်းပါ။
ကြိုးများ၊ ခလုတ်များ၊ နှင့် ပြသသည့် မျက်နှာပြင်များကဲ့သို့သော အခြားအစိတ်အပိုင်းများကို ချိတ်ဆက်ပါ။
အဓိကအချက်များ-
PCB သို့မဟုတ် အခြားအစိတ်အပိုင်းများ ပျက်စီးခြင်းမှ ရှောင်ရှားရန် တပ်ဆင်မှု တိကျမှုကို သေချာပါစေ။
တည်ငြိမ်ပျက်စီးမှုကို ကာကွယ်ရန် anti-static ကိရိယာများကို အသုံးပြုပါ။
(၂) Software မီးလောင်ခြင်း။
အဆင့်များ-
firmware သို့မဟုတ် software ကို PCB ၏မှတ်ဉာဏ်ထဲသို့ထည့်ပါ။
ဆော့ဖ်ဝဲ ပုံမှန်အတိုင်းလည်ပတ်ကြောင်း သေချာစေရန် မီးလောင်မှုရလဒ်များကို စစ်ဆေးပါ။
အဓိကအချက်များ-
မီးလောင်သည့်ပရိုဂရမ်သည် ဟာ့ဒ်ဝဲဗားရှင်းနှင့် ကိုက်ညီရပါမည်။
အနှောင့်အယှက်များကို ရှောင်ရှားရန် မီးလောင်နေသော ပတ်ဝန်းကျင်သည် တည်ငြိမ်ကြောင်း သေချာပါစေ။
(၃) စက်တစ်ခုလုံး စမ်းသပ်ခြင်း။
အဆင့်များ-
စုစည်းထားသော ထုတ်ကုန်များပေါ်တွင် လုပ်ဆောင်နိုင်သော စမ်းသပ်မှုများ ပြုလုပ်ပါ။
အသွင်အပြင်၊ စွမ်းဆောင်ရည်နှင့် ယုံကြည်စိတ်ချရမှုကို စစ်ဆေးပါ။
အဓိကအချက်များ-
စမ်းသပ်သည့်အရာများသည် လုပ်ဆောင်ချက်အားလုံးကို အကျုံးဝင်ရပါမည်။
စမ်းသပ်မှုဒေတာကို မှတ်တမ်းတင်ပြီး အရည်အသွေး အစီရင်ခံစာများ ဖန်တီးပါ။
(၄) ထုပ်ပိုးခြင်းနှင့် ပို့ဆောင်ခြင်း။
အဆင့်များ-
အရည်အချင်းပြည့်မီသော ထုတ်ကုန်များ၏ တည်ငြိမ်သော ထုပ်ပိုးမှု။
တံဆိပ်တပ်ပါ၊ ထုပ်ပိုးပြီး တင်ပို့မှုအတွက် ပြင်ဆင်ပါ။
အဓိကအချက်များ-
ထုပ်ပိုးမှုသည် သယ်ယူပို့ဆောင်ရေးနှင့် သိုလှောင်မှုလိုအပ်ချက်များနှင့် ကိုက်ညီရမည်။
အလွယ်တကူ ခြေရာခံနိုင်စေရန်အတွက် ပို့ဆောင်မှုဆိုင်ရာ အချက်အလက်များကို မှတ်တမ်းတင်ပါ။

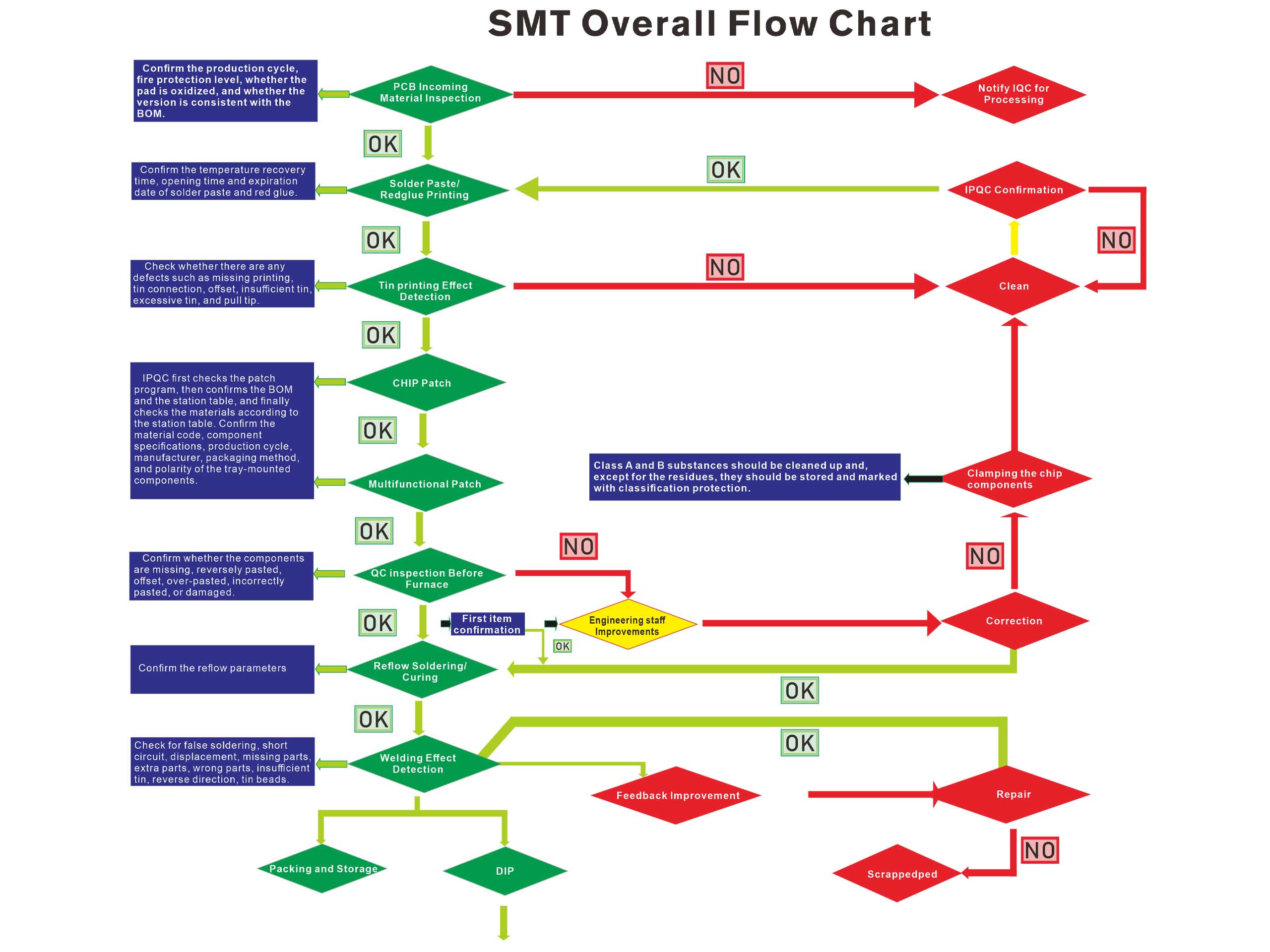
5. အဓိကအချက်များ
ပတ်ဝန်းကျင်ထိန်းချုပ်မှု-
အငြိမ်လျှပ်စစ်ကို တားဆီးပြီး ငြိမ်ဆန့်ကျင်ပစ္စည်းနှင့် ကိရိယာများကို အသုံးပြုပါ။
စက်ပစ္စည်း ပြုပြင်ထိန်းသိမ်းမှု-
ပရင်တာများ၊ နေရာချထားသည့်စက်များ၊ ပြန်ထွက်မီးဖိုများ၊ လှိုင်းဂဟေမီးဖိုများကဲ့သို့သော စက်ပစ္စည်းများကို ပုံမှန်ထိန်းသိမ်းပြီး ချိန်ညှိပါ။
လုပ်ငန်းစဉ် ပိုမိုကောင်းမွန်အောင် ပြုလုပ်ခြင်း-
အမှန်တကယ်ထုတ်လုပ်မှုအခြေအနေအရ လုပ်ငန်းစဉ်ဘောင်များကို ပိုမိုကောင်းမွန်အောင်ပြုလုပ်ပါ။
အရည်အသွေးထိန်းချုပ်မှု-
လုပ်ငန်းစဉ်တစ်ခုစီသည် အထွက်နှုန်းသေချာစေရန် တင်းကျပ်သော အရည်အသွေးစစ်ဆေးခြင်းကို ခံယူရမည်ဖြစ်သည်။